Firma IMA Schelling Group opracowała nowatorskie rozwiązanie dla włoskiego klienta, umożliwiające w pełni zautomatyzowaną produkcję wysokiej jakości profili krawędziowych. Dzięki specjalnemu systemowi oklejania krawędzi, możliwe stało się tworzenie frontów meblowych o minimalistycznym designie, coraz częściej wybieranych przez współczesnych konsumentów.
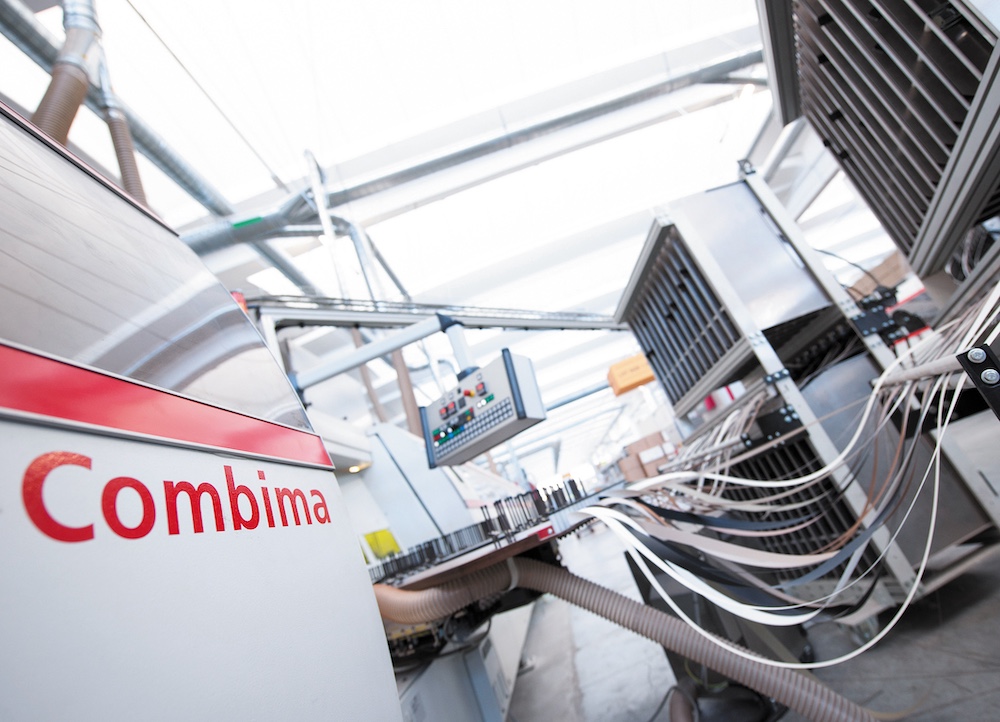
Maszyna do obróbki formatu i krawędzi Combima została dostosowana do wymagań włoskiego klienta przez IMA Schelling
Zdjęcie: IMA Schelling Group
Fronty z uchwytami czy bez? Trend ku minimalizmowi
Wybór między frontami z uchwytami a tymi bez uchwytów to dziś jedna z kluczowych decyzji przy projektowaniu kuchni. Coraz więcej osób decyduje się na fronty bez uchwytów, które nadają wnętrzom nowoczesny, czysty wygląd.
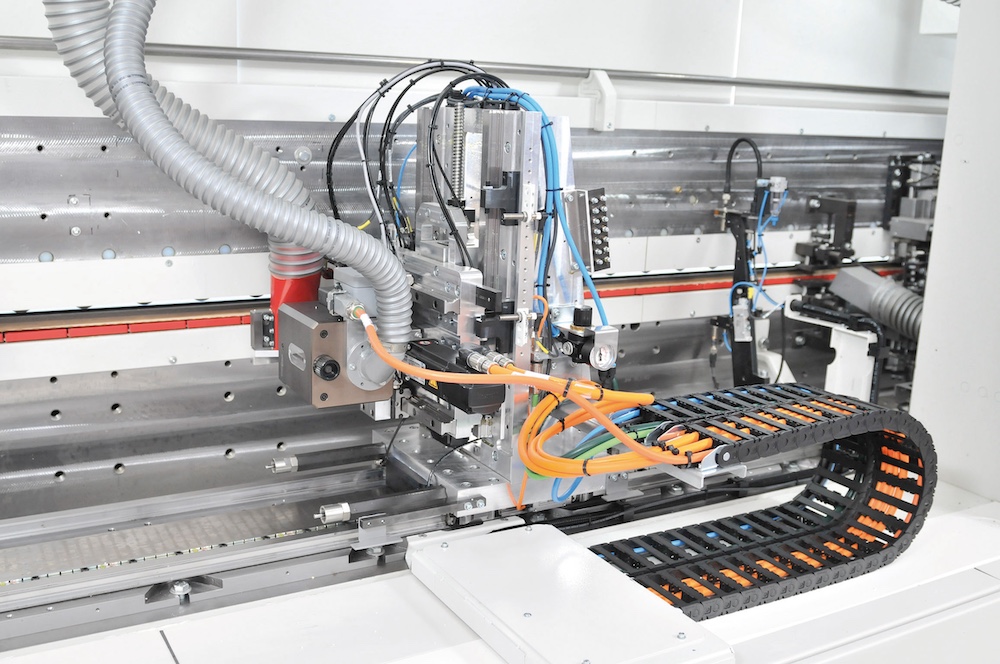
Zdjęcie: IMA Schelling Group
Jednak produkcja takich frontów stawia przed technologią obróbki krawędzi szczególne wymagania. Dotychczas stosowano dwie metody:
- Aluminiowe profile mocowane na krawędziach – drogie i czasochłonne.
- Frezy w płytach MDF – wymagające dodatkowego malowania.
– Obie metody są kosztowne i skomplikowane – wyjaśnia Dennis Reddig, Product Manager Edge Processing w IMA Schelling.
Maszyna do czterech typów profili i krawędzi prostych
W odpowiedzi na potrzeby włoskiego klienta, IMA Schelling stworzył specjalną maszynę do obróbki krawędzi, zdolną do w pełni zautomatyzowanego wykonywania zarówno krawędzi prostych, jak i profilowanych. Wymagane były cztery rodzaje profili:
- J-profil
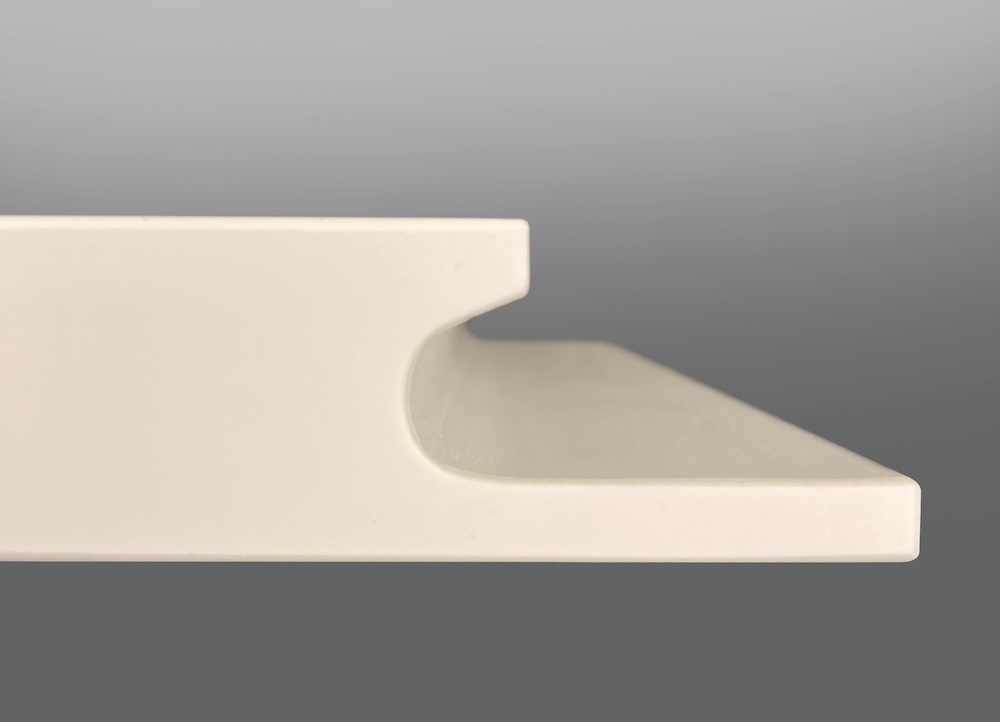
Zdjęcie: IMA Schelling Group
- C-profil

Zdjęcie: IMA Schelling Group
- Profil skośny

Zdjęcie: IMA Schelling Group
- Profil wpustowy
Największym wyzwaniem było oklejanie krawędzi w przypadku profili J i C. – Przeprowadziliśmy liczne testy z różnymi materiałami i metodami aplikacji kleju, zanim osiągnęliśmy optymalne rezultaty – mówi Reddig.
Wyzwanie nr 1: Dobór materiału okleinowego
Standardowe materiały do softformingu (oklejania kształtów krzywoliniowych) są cienkie i elastyczne, ale w tym przypadku ich struktura była widoczna na powierzchni płyt wiórowych.
– Musieliśmy zwiększyć grubość okleiny – tłumaczy Reddig. Jednak grubsze materiały generują większe siły sprężystości, co utrudnia ich precyzyjne dopasowanie do profili.

Zdjęcie: IMA Schelling Group
Wyzwanie nr 2: Aplikacja kleju
W tradycyjnych maszynach do oklejania, klej nakładany jest najpierw na płytę, a dopiero potem dociskana jest okleina. W przypadku profili J i C ten sposób był niewystarczający.
– Ostatecznie połączyliśmy dwie metody: aplikację kleju na okleinę i na płytę w kluczowych obszarach – wyjaśnia Reddig.
Dodatkowo, należało precyzyjnie dobrać ilość kleju – zbyt mała powodowała słabą przyczepność, a zbyt duża wymagała czasochłonnego czyszczenia.

Zdjęcie: IMA Schelling Group
Wyzwanie nr 3: Grubość i giętkość okleiny
Klient wymagał zastosowania materiałów o grubości 0,6–1,0 mm, które musiały być wyginane pod kątem bliskim 90°.
Rozwiązaniem okazało się miejscowe podgrzewanie materiału oraz zastosowanie mechanicznych narzędzi do nacinania, ułatwiających formowanie.
Combima – wielofunkcyjna maszyna do produkcji frontów

Zdjęcie: IMA Schelling Group
Wszystkie te rozwiązania zostały zintegrowane w maszynie Combima, przystosowanej do produkcji w systemie partii jednostkowej (batch size 1). Dzięki temu klient otrzymał:
- W pełni zautomatyzowaną linię do produkcji frontów z różnymi profilami.
- Pięć różnych kształtów krawędzi w automatycznym cyklu produkcyjnym.
- Zaawansowane jednostki wykończeniowe, takie jak:
- I-KFA (zaokrąglanie wewnętrznych narożników),
- skrobaki profilowe i płaskie,
- polerki i szczotki.
Maszyna ma ponad 40 metrów długości, co czyni ją wyjątkową w branży meblarskiej. – To specjalistyczne rozwiązanie, prawdziwy unikat – podsumowuje Reddig.
IMA Schelling – kompleksowe rozwiązania dla przemysłu meblarskiego
IMA Schelling Group to światowy lider w produkcji maszyn dla przemysłu drzewnego, tworzyw sztucznych i metali. Firma oferuje:
- Innowacyjne systemy cięcia, wiercenia i oklejania krawędzi.
- Automatyzację produkcji mebli w systemie batch size 1.
- Doradztwo i rozwiązania cyfrowe dla zoptymalizowanej produkcji.
Dzięki 17 oddziałom na świecie i ponad 1850 pracownikom, IMA Schelling dostarcza zaawansowane technologie, spełniające nawet najbardziej wymagające potrzeby klientów.
Chcesz dowiedzieć się więcej o nowoczesnych maszynach dla meblarstwa? Odwiedź: https://www.imaschelling.com/pl/
Ww. materiał jest udostępniony na zasadzie publikacji własnej.
© Branżowa Agencja Informacyjna iPortale.pl Sp. z o.o. – portal maszynydlameblarstwa.pl| Wszelkie prawa zastrzeżone.